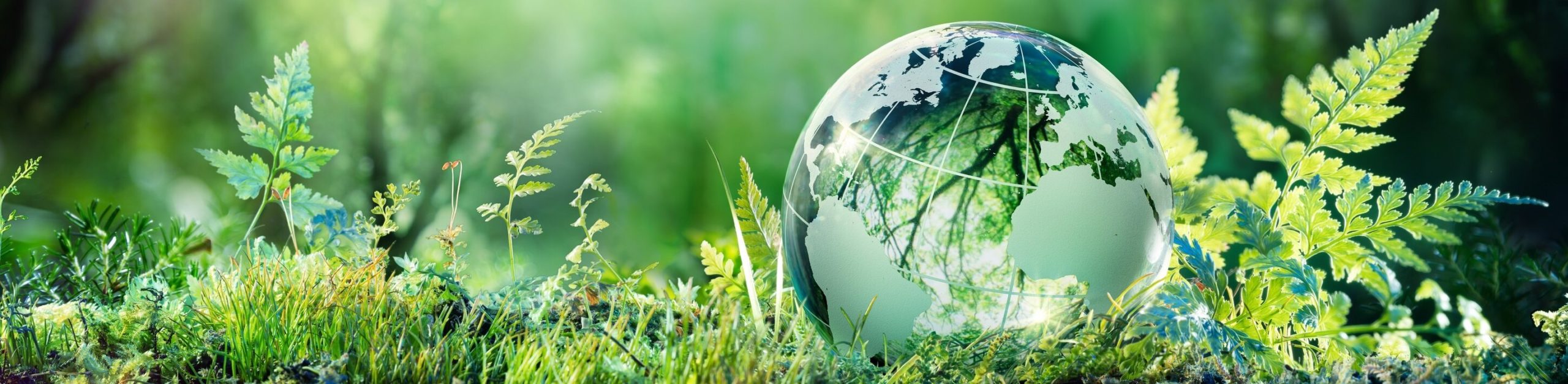
What Is Industrial Hygiene?
What is Industrial Hygiene? Essentially, Industrial Hygiene is the science of protecting and enhancing the health and safety of people at work and in their communities. Health and safety hazards cover a wide range of chemical, physical, biological and ergonomic stressors. Those dedicated to anticipating, recognizing, evaluating and controlling those hazards are known as Industrial Hygienists.
More specifically, a Certified Industrial Hygienist (CIH) is an Industrial Hygienist who has met very rigorous certification standards.
Industrial Hygiene Requires a Rare & Highly Sought-After Skillset
There are only 7,500 CIHs in the United States (covering 60,000 factories and 12,750,000 workers – a very low CIH to Factory/Employee ratio). Many of the CIHs are employed by OSHA. More than 40% of the OSHA compliance safety and health officers are knowledgeable industrial hygienists who inspect facilities for compliance.
Do You Need Help From a Certified Industrial Hygienist for Your Facility?
It definitely helps. And preferably at the beginning, when you’re establishing your policies and procedures. Of course, it’s best to be proactive and not wait until you’re in a position where you have to develop a plan of action stemming from a worksite inspection or to respond to a reported complaint, release, injury, or in the worst-case scenario – death. Also, due to the large number of industrial hygiene inspectors at OSHA, you can be at a big disadvantage if you have not had a CIH evaluate hazard exposures at your facility.
.
Rindt-McDuff Associates’ Industrial Hygiene Services
RMA has Certified Industrial Hygienists (CIHs) available to help you meet OSHA safety mandates. We help employers develop effective safety and health programs by:
- Performing a Worksite Analysis to identify what jobs and work stations are sources of potential hazards through identification of exposures, problems, and risks;
- Controlling Hazards through the use of engineering controls, work practice controls, and administrative controls;
- Testing and evaluating the workplace for hazards and dangers such as air contaminants, dust, fumes, mists (aerosols), fibers, and gasses (vapors);
- Making recommendations for appropriate corrective actions;
- Anticipating potentially hazardous situations and providing a plan of action to avoid them;
- Training and educating employees about job-related risks; and
- Developing a program to ensure workers properly follow health and safety procedures.
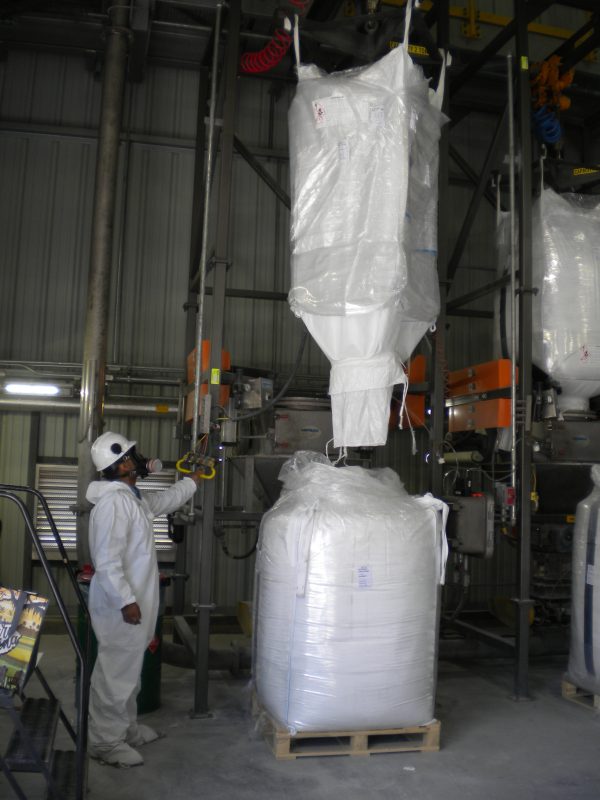
What’s Next?
Be proactive. Get ahead of the OSHA inspectors by anticipating, recognizing, evaluating, and controlling any hazardous factors in your environment before a complaint or injury is reported.
Click below to speak with one of our safety specialists today.